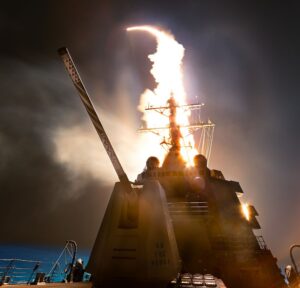
The Navy in the past few months has awarded six contracts to four companies to design, build, and test rocket motors and related technology for the Standard Missile (SM)-6 as it moves forward with extending the range and capabilities of the ship-fired anti-air missile. Navy and industry officials have said that the design and development awards could also lead to expanding the industrial base for solid rocket motors (SRMs). The Aerojet Rocketdyne segment of L3Harris Technologies [LHX] makes the Mk…