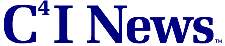
February 28, 2008
Table of Contents
- DHS Accepts First Section of Boeing-Developed Electronic Border Fence
- Northrop Grumman In Second Year of Next Generation ABIS Development
- Northrop Grumman To Provide MEADS Navigation/Localization System
- General Dynamics Protests Lockheed Martin CAMC2 Win
- Lockheed Martin, Flight Safety International, Partner Microsoft For ESP Platform
- EMALS Will Bring Changes To Carrier Flight Ops
- Raytheon To Pursue GOES-R Ground Segment Work
- General Dynamics UK Begins Latest Bowman Communications Enhancements
- Kratos To Acquire SYS Technologies
- Singapore Air Force Taps IAC For Advanced Hums For AH-64D Apaches
- Northrop Grumman Demonstrates Advanced EHF Satellite Interface With Terminals
DHS Accepts First Section of Boeing-Developed Electronic Border Fence
The Department of Homeland Security (DHS) last weeky fully accepted the first installment of an integrated electronic border security system that includes a common operating picture for Border Patrol agents responsible for manning a 28-mile stretch of the United States border with Mexico, Homeland Security Secretary Michael Chertoff said on Friday.
Final acceptance by DHS had been delayed since last summer due to difficulties in integrating the various sensors and creating the common operating picture that is expected to allow border security officials to spot illegal immigration activity and respond quickly. Project 28, as the first installment of the Secure Border Initiative integrated technology (SBInet) installment is known, covers a section of the Border Patrol’s Tucson, Ariz., sector.
Despite the delays in the official handoff of the system from Boeing [BA], which is developing SBInet for DHS, the system has been in operational use.
“I have personally witnessed the value of this system and I have spoken directly to Border Patrol agents who are involved in operating that system over the last few months and who have seen it produce actual results in terms of identifying and allowing the apprehension of people who are illegally smuggling across the border,” Chertoff said.
Due to the delays in meeting the original contract delivery milestones, Boeing agreed to a $2 million credit refund to DHS. The original P28 task order was for $20 million but Boeing’s take is now $18 million, DHS said.
Chertoff noted that SBInet is not a “once size fits all” solution for every section of the U.S. border, north and south. He said the P28 model will have to be adjusted depending on the unique requirements of each stretch of border. In some places ground-based radar will be sufficient, he said. Chertoff added that this year DHS plans to add 34 more ground based mobile surveillance systems throughout the border from the current six.
Before DHS and Customs and Border Protection decide which stretch of border Boeing will have to address next under SBInet, the company is expected to make some spiral upgrades to P28, including going from the current eight mobile sensor towers to fixed sites. Moreover, companies that believe they have technological solutions, such as imaging sensors, that could improve on the current P28 system, will have their technology examined at Boeing’s system integration laboratory in Huntsville, Ala., as possible upgrades to P28 in the coming months.
In addition to the integrated electronic fencing, DHS is in the process of installing physical fencing along the southwest U.S. border. So far, 302 miles of vehicle and pedestrian fencing has been installed and by the end of this year that will stretch to 670 miles, Chertoff said.
DHS is also buying additional General Atomics Aeronautical Systems Predator Unmanned Aerial Vehicles to help patrol the borders, Chertoff said. Right now, CBP has three of the air vehicles with plans to buy three more.
Northrop Grumman In Second Year of Next Generation ABIS Development
Northrop Grumman [NOC] has begun to get the computer architecture in place for the Defense Department’s new biometric database and, by the end of this year, is expected to have the computer system ready to begin adding biometric search capabilities, the Army project manager overseeing the work said recently.
Northrop Grumman is currently in the second year of developing the next generation Automated Biometric Identification System (ABIS), which in addition to housing fingerprints will also store other biometric records. The second year is actually the first of four option years for the contract. Northrop Grumman was selected for the award in November 2006 although the announcement was delayed two months due to a protest by Lockheed Martin [LMT], the losing bidder.
Late this year, a new “supercomputer” should be built and “then the capabilities start coming after that,” Col. Ted Jennings, project manager for DoD Biometrics, told sister publication Defense Daily in an interview. The original, or prototype ABIS, which was developed and operated by Lockheed Martin, is fingerprint based and accepts information in a certain format. With the next-generation system, which will likely be renamed, “we’re putting it into a different enhanced format that’s going to allow the functions to be scalable and also to have the capability to put in the different [biometric] modalities,” he said.
Fingerprint technology will be the baseline for the new version of ABIS. What modalities come next will depend on user requirements, Jennings said.
“And so we’re working with the user requirement community out of TRADOC (Army Training and Doctrine Command) and the Biometrics Task Force to figure out exactly what they want to go into this new capability,” Jennings said.
Meanwhile, Northrop Grumman is operating the prototype ABIS. That system is used by DoD to see if fingerprints of captured insurgents and potential terrorists match against records already on file to identity who our soldiers may have apprehended or come across. ABIS is also used to see if persons applying for work on U.S. military installations may previously have been associated with criminal, insurgent or terrorist activity.
As to when DoD will be able to transition to the next generation ABIS, Jennings said his office continues to work with the Army and the Office of Secretary of Defense on the various capabilities the system will have and when.
Northrop Grumman To Provide MEADS Navigation/Localization System
Northrop Grumman [NOC] Feb. 19 announced MBDA Italia has selected the company to provide the navigation and localization system for the U.S., German and Italian Medium Extended Air Defense System (MEADS) program.
Terms of the contract were not disclosed.
Under the contract, Northrop Grumman’s Italian subsidiary, Northrop Grumman Italia, will be responsible for the navigation and localization system that supports the radars and launchers which are part of the MEADS program.
“We have been providing military navigation systems and services to the Italian government as well as other European nations for nearly 50 years,” Giovanni Morelli, business development director for Northrop Grumman Italia, said. “The proven capabilities of our navigation systems will help enable MEADS to offer significant improvements over existing defense systems.”
MBDA Italia is part of MEADS International, a multinational joint venture including Lenkflugkorpersysteme (LFK) in Germany and Lockheed Martin [LMT] in the United States.
The design and development phase of the MEADS program began in 2004 and is now in the design and development phase. It recently successfully completed its preliminary design review and is moving into detailed design work aimed at a critical design review next year (Defense Daily, Feb. 15). Seven increasingly complex flight tests are scheduled for 2011 through 2013.
MEADS is expected to replace U.S. Patriot systems, Italy’s Nike Hercules systems, and to supplement and eventually replace Patriot systems in Germany. The mobile, 360 degree protective system is planned to protect maneuvering forces as well as fixed installations against current and next-generation missile threats, unmanned aerial vehicles and aircraft.
Northrop Grumman Italia is part of the Navigation Systems Division, headquartered in California. Northrop Grumman Italia provides a variety of navigation systems and products used in air, naval and land-based applications and it serves as a prime contractor for domestic Italian and European collaborative programs.
In Europe, Northrop Grumman operates from locations in France, Germany, Italy and Norway.
The MEADS total program contract is valued at about $3.4 billion, of which about $2 billion goes to work in the United States, $500 million to work in Italy, and other funds to Germany. The United States funds 58 percent of the MEADS program, Germany provides 25 percent and Italy 17 percent as partners in the NATO Medium Extended Air Defense System Management Organization (NAMEADSMO). Its program management agency, NAMEADSMA, is located in Huntsville, Ala.
General Dynamics Protests Lockheed Martin CAMC2 Win
General Dynamics [GD] C4 Systems Feb. 8 protested to the Government Accountability Office the Army’s award to Lockheed Martin [LMT] of production and support for the Common Army/Marine Command and Control (CAMC2).
“It would be inappropriate to comment because the matter is in litigation,” a General Dynamics spokeswoman said.
The contract was awarded Feb. 1.
The Army Materiel Command on behalf of Army Communications Electronic Life Cycle Management Command Acquisition Center awarded the contract for the CAMC2. The system is part of the Army Mounted Battle Command On The Move (MBCOTM) Program and the Marine’sCommand and Control On The Move Network Digital Over The Horizon Relay (CONDOR) Program.
The five-year, Indefinite Delivery, Indefinite Quantity (IDIQ) contract has two one-year options including both Firm-Fixed Price (FFP) and Time and Materials (T&M) line items.
CAMC2 consists of an A-Kit and B-Kit installation on certain vehicles, such as General Dynamics’ Stryker, and is made up of Non-Developmental Item, rugged Commercial Off-the- Shelf, government furnished material, government furnished equipment and government furnished information.
Lockheed Martin, Flight Safety International, Partner Microsoft For ESP Platform
Microsoft [MSFT] took another step forward into the defense and aviation arena with its simulation ESP Platform, announcing two new industry parners: Lockheed Martin [LMT] and Flight Safety International.
“As a simulation platform we can really help reduce the significant investments that these partners are making when they’re basically required to maintain their own multiple proprietary visual simulation systems,” Shawn Firminger, studio manager, Microsoft ACES Studio, told sister publication Defense Daily. Related to that, is based on our unique pricing model, it’s very cost efficient. It’s flexible. It’s going to be very easy to deploy solutions on top of it.”
Microsoft sees this as a “game changer” that will “accelerate the COTS-based movement,” he said. The intent is to provide a common simulation platform consistent across all industry.
In late November, Microsoft announced new partners including SAIC [SAI], Northrop Grumman [NOC] and CAE [CGT] that will build custom visual simulation solutions on the ESP platform (Defense Daily, Nov. 29). That announcement followed the Nov. 14 debut of Microsoft ESP that brings immersive games-based technology to training and learning, decision support and research and development modeling for military and commercial aviation organizations.
Firminger said companies can see the ESP platform’s capability as a rapid prototyping device where they can use their own expertise and quickly build on the ESP platform for a customer’s requirement.
“This group has been around over 25 years, building simulations for that length of time, building and delivering them to the entertainment world, and we’ve seen seen our technology change a lot,” Firminger said. “We use technology to solve our business problems and it’s really following customer demand.”
Microsoft sees the opportunity to enter the market with the ESP as a common simulation platform.
“We at Microsoft know how to build platforms, pretty robust platforms. ESP version 1 is actually pretty far along and pretty advanced,” he said.
Microsoft ESP consists of an underlying PC-based simulation engine built on the nearly 25 years of knowledge for Flight Simulator, with development tools and content that models the entire Earth. High fidelity 3D visual imagery is part of it, so is a configurable user-adjustable weather system, accurate vector data and geography that can be custom tailored.
An After Action Review feature allows recording and review of every action made during a session. Additionally, custom missions can be created to tailor simulations to specific training goals.
“We provide a base world to start, with a common production pipeline,” Firminger said.
On the entertainment side of the business, for Flight Simulator, one can find more than 200,000 different pieces of content for new functions that can be added to the game– aircraft, scenery, weather. These have been created and shared by the community. It’s possible something similar could evolve in the defense area.
Since the November roll-out, there’s been a lot of interest in the ESP Platform’s potential, he said. Earlier this week he spoke at a conference and was “swamped” afterward by a variety of people wanting to know more.
“Once people understand what we’re doing and have a chance to see the tech, that’s when the lightbulb goes on,” he said.
The software can be used by foreign customers, he said. “We’ve intentionally done that.”
The way it works is that Microsoft licenses the same basic ESP Platform to customers and partners, but retains ownership, while customers build their unique solutions on the platform.
“We really think it will open up and expand the opportunities for new training scenarios,” he said. For example, not only for simulations to train pilots, but also for aircraft maintenance personnel. “Now there are opportunities to think about how to use modeling and simulation.”
Research now out indicates that today’s workforce, entering the market, or the under 40 group, is very familiar with immersive technology, he said. For that group, if simulation is introduced into the learning environment, scores go up a minimum of 20 points.
Firminger said while Microsoft ESP version one focuses on civil and military aviation training and decision support, Version Two will add support for vehicle operator training, ground operations and other scenarios. Next, the team will focus on building out an even richer and more complex set of location details–on the water, under the water, inside buildings and cities–gradually moving more deeply into core scenarios that enable Microsoft ESP partners to meet the needs of their customers in this growing market.
The platform is not the solution, but an important piece of the work. The customer must solve the problem, “tap into the ecosystem we want to see flourish around the platform so solutions can be created,” Firminger said.
EMALS Will Bring Changes To Carrier Flight Ops
The Navy is confident the Electro Magnetic Aircraft Launch System (EMALS) being designed for CVN-21 will help reduce manning on carriers, increase aircraft sortie rates, and provide a system that will be capable of launching the variety of aircraft planned for the future.
Topside, not much will change with the addition of EMALS. Aircraft will continue to be hooked up to a shuttle, then to the catapult, and shot down the deck to get up to speed for launch.
Catapult operators launching aircraft will probably not notice much of a difference, either. There will be some new displays because they will be looking at different information now, Capt. Stephen Rorke, program manager for aircraft launch and recovery equipment, told sister publication Defense Daily in a recent interview.
Operators will still have to worry about the weights of the aircraft and the settings. But now, instead of setting steam selector valve settings based on the weight of the aircraft, they will tell the computer how much power is needed, what the end speed is, and the system has the ability to compensate for all kinds of things to make sure that aircraft achieves that end speed so that it launches and flies safely, he said.
“All the magic, what is going on behind the curtain, is all down below [deck],” Rorke said. “Everything is different. It is not a kind of a band-aid or retrofit on the steam [catapult].”
The basic design is made up of multiple subsystems, he said. “But if you really get right down to it, there is an energy storage subsystem and then there is the launch motor to actually get the aircraft off.”
“There are other subsystems to support all that but if you get down to the basics we store the energy, in this case in rotating machines,” Rorke explained, rather than in steam accumulators, which is how a steam catapult system stores power.
With EMALS, when an operator pushes the button to initiate the launch sequence, the energy from those machines is sent through a distribution network and formed into the correct wave forms to feed the linear motor, Rorke added. “Basically this is an electromagnetic driven linear launch motor.”
The reason the Navy transitioned to EMALS in CVN-21 was to change a lot of the technology on the ship and bring it up to the latest standards, with the idea of making it even simpler, more reliable, with less impact to the ship, Rorke said.
“One of the advantages of this, we no longer have to take steam from the engineering places all the way up to the topside to launch the aircraft. All we have to do is move electricity around,” he said.
Another advantage of EMALS is that it’s a lot more flexible in adapting to the needs of the current aircraft plus what the Navy is projecting in the future, in particular the F-35 Joint Strike Fighter (JSF) and Unmanned Combat Air Systems (UCAS), Rorke added.
“If you think about the fact we are building this carrier that will deliver in 2015, with a 50-year lifecycle, what are we going to be seeing out there in 2085? This is the first of the new class and so the intent is we will build a few more of these things. So if you think about it, this system is going to be out there for a long time 75 to 100 years into the future,” he said “So what is going to be out there in the future?”
EMALS can be tailored to the launch forces better than could be done with steam catapults, Rorke said.
“There is a lot of technology in steam…how the launch valve opens, how much energy is put into the cylinders…but there is only a limit to what you can do without making that system extremely overly complicated, more complex, and therefore more prone to having a failure mode,” he added. “The idea with [EMALS] is that I have inherent flexibility built into this thing. I can tailor my launch forces to the aircraft at hand.”
Moving toward an electro magnetic catapult system will also impact operational capability, Rorke said.
One condition of EMALS is that it had to demonstrate that its availability was at least as good, if not better, than steam catapults, he noted. “That is what we are designing for.”
The mean time between failures, the meantime between repairs, are better than steam, Rorke said.
“All of those are design parameters that have gone into this whole system.”
The Navy is designing CVN-21 to have a crew size that will be approximately 1,200 sailors fewer than a Nimitz-class carrier (Defense Daily, July 10, 2007). In order to attain a smaller crew size, many of the new systems must be able to operate without human intervention. “So the ship itself has a lot of smart technologies being put into it. EMALS is one of them.”
For EMALS to be operated with fewer people, a number of things have to be done, he added.
For example, the system needs to be able to monitor itself and tell maintainers what’s wrong, and point them in the right direction to make repairs.
“Because I have better availability, because I can repair it faster, because the diagnostic system that is being built into it will tell me the status, I can get more sorties per day off the ship. That was one of those other design considerations in the CVN-21 program–increase the sortie generation rate,” Rorke said.
EMALS will first be installed and used on the USS Gerald Ford (CVN-78). The system will not be retrofitted on to other carriers, Rorke noted.
The first delivery of subsystems to the Ford will occur in 2011, Rorke said. Because EMALS is part of the ship, its Initial Operational Capability coincides with the Ford‘s, which is scheduled to be delivered in the 2015 time frame, he added.
Until then, EMALS will undergo years of testing at Naval Air Engineering Station Lakehurst, N.J.
Lakehurst is the center of excellence for aircraft launch and recovery equipment, Rorke said.
“It has been and remains the hub of engineering for aircraft launch and recovery equipment. They have test tracks for arresting gear testing, they have steam catapults on the test runway, and now on the opposite side of the runway they have EMALS going in,” he said.
About four years ago, the Navy held a competition for an electromagnetic launch system. The competitors had to build a full-scale but short length system and demonstrate it using components that were not necessarily militarized or that could fit into a ship, Rorke said. Based on the Preliminary Design System, the Navy awarded General Atomics Aeronautical Systems the EMALS contract. “Their design is essentially what we are building now for full scale.”
Although the catapult track itself was about half the length of what would go on a carrier’s deck and the power available with commercial generators was not what the Navy was going to use on the ship, nonetheless General Atomics was able to demonstrate within the length of track they built that they could get weights up to 100,000 pounds accelerated and they could get dead loads or lightweights up to 180 knots, Rorke said.
Since then the Navy has conducted thousands of shots using dead loads and lightweight loads, at various speeds, to show it can be done.
“That design is what we have spent the last couple of years refining and shipboard ‘navalizing’ it, if you will, making it fit within the available spaces, finalizing all the component selections, scaling it up to the catapult track on the ship, and probably the more interesting of our challenging pieces was the generator itself,” Rorke added.
The ship set will contain 12 generators in a shared arrangement to drive all the catapults, he said.
“That generator system, for its power and size, is a remarkable piece of equipment. Probably one of the most power dense generators ever built,” Rorke said. “That is a big piece, the heart of this…storing that energy so they can release [it] in the two-and-a-half seconds it takes to do a launch. Taking that much energy up to 102 megajoules of energy to get the aircraft off to the highest speed possible. It’s pretty phenomenal.”
Now the plan is to test the system at Lakehurst and make it compatible for the aircraft that currently exist in the Navy’s inventory, he added.
One of the biggest tasks in the test program will be to verify all the models, make sure the assumptions of the design are valid and tailor the profiles–start building the first launch bulletins for the aircraft, Rorke said.
“So part of the full-scale testing up at Lakehurst will be to do live launching in ’09,” he added.
Raytheon To Pursue GOES-R Ground Segment Work
Raytheon [RTN] will head a team of companies and universities to pursue a National Oceanic and Atmospheric Administration (NOAA) next-generation Geostationary Operational Environmental Satellite R series known as the GOES-R ground segment.
The GOES program provides the nation with continuous severe weather sentinels in space.
GOES-R satellites will provide critical weather observations for severe weather events such as hurricanes, and enhance observational capabilities for climate, oceans and coasts, and the space environment.
GOES-R also will advance environmental data collection and analysis.
Raytheon GOES-R team members include Lockheed Martin [LMT], Arctic Slope Regional Corp., Omitron, Orbital Network Engineering, Silicon Graphics Inc., STC-METSAT, SM Resources Corp., RT Logic, and Photon Research Associates, a wholly owned subsidiary of Raytheon.
“As the prime contractor, Raytheon will lead this team of foremost experts in the fields of ground segment technology and system integration,” said Michael Keebaugh, president of Raytheon Intelligence and Information Systems (IIS). “Together, these trusted partners bring more than 60 years of experience in providing environmental processing systems.”
The team also includes the University of Oklahoma and The University of California–Los Angeles, in the areas of data mining, training, development, modeling and simulation, scene generation, and data verification and validation.
General Dynamics UK Begins Latest Bowman Communications Enhancements
General Dynamics [GD] United Kingdom Limited has begun rolling out enhanced communications and data capabilities for the Bowman tactical communications system.
The U.K. Ministry of Defence has formally accepted the latest increment of Bowman, BCIP5, which stands for Bowman and ComBAT, Infrastructure and Platform BISA (CIP).
Bowman is used by all three of the armed services, and BCIP4 is already providing battle-winning capability on operations in Iraq and Afghanistan by improving the speed, quality and security of tactical communications and enhancing situational awareness.
General Dynamics UK has already integrated the Bowman system into more than 12,000 British Army vehicles, from Challenger tanks to Land Rovers, enhancing the communications abilities of soldiers on foot, ships, helicopters, and operational headquarters.
The Acceptance and Release decision for BCIP5 was made on Jan. 31 and gave the approval to commence fielding.
The BCIP5 will:
deliver an enhanced robust, resilient and mobile tactical internet with improved situational awareness for commanders at all levels;
increase use of data-networking, in conjunction with new Battlespace Management tools, enhancing the information flow between units and headquarters staff; and
enable each Bowman radio fitted with GPS to send its Own Station Position Report (OSPR), to produce a picture of where friendly forces are in the battlespace, improving situational awareness.
Following a successful Operational Field Trial and formal acceptance meetings with the MoD, the roll-out of BCIP5 has begun with the uplift of the Royal Navy’s Type 22 frigate HMS Chatham and Type 23 frigate HMS Monmouth.
A three-year roll-out will enable the armed services to train soldiers and update practices to get the best use of BCIP5 and absorb the new capability, while continuing to deliver operational commitments.
Speaking for the MoD, Commodore Jay Hart, Bowman And Tactical Communications & Information Systems (BATCIS) Integrated Project Team leader, said: “Bowman is already proving its worth on operations, and we are very pleased that BCIP5 has achieved acceptance. When it is rolled out the new Bowman increment will help our armed forces improve the way they share information and work together on operations.”
Sandy Wilson, president and managing director of General Dynamics UK, said: “Since we took on Bowman in 2001 we have delivered significant and vital capability to the soldiers on the ground. We are pleased that BCIP5 has been given the thumbs-up, and we will continue working closely in partnership with the MoD to roll it out to our armed forces over the next three years.”
General Dynamics UK has been established as a prime contractor and systems integrator in the United Kingdom for over 40 years, employing about 1,700 people at eight facilities. General Dynamics UK leads a key MoD Defence Technology Centre research consortium and, together with a growing C4I export programme, plays a central role manufacturing and developing technology to deliver Network Enabled Capability and ISTAR in the battlespace.
Kratos To Acquire SYS Technologies
Kratos Defense & Security Solutions [KTOS] said yesterday it plans to acquire SYS Technologies [SYS] in a stock-for- stock transaction that will expand the companies portfolio of C4ISR and combat systems service and solution offerings.
The deal is expected to close by the end of June and is subject to the approval of shareholders of both companies. Kratos, which provides engineering, information technology services and war fighter solutions for the federal government and for state and local agencies, expects the combined company to have an annualized revenue run rate of nearly $400 million by the end of this year.
Kratos said the acquisition is complementary and has no competitive overlap. Both firms are based in San Diego. Because both firms are public companies, Kratos expects to immediately achieve cost savings once the deal is done.
“In an ever-increasing competitive environment, it is absolutely critical that we increase scale and critical mass for a number of reasons,” Cliff Cooke, president and CEO of SYS Technologies, said in a statement. “This merger allows SYS to continue its successful growth plan and offers our customers a broader range of complementary services and solutions. Although SYS is successfully executing its strategic plan, industry conditions, competitive factors and financial considerations make this merger with Kratos an extremely positive move from a strategic, industry, customer and employee perspective, especially since the SYS business is a smaller size public company, with its operating margins negatively impacted by the high costs associated with operating as a public company.”
The deal will help Kratos expand its customer footprint within DoD and the federal government, and geographically. Kratos also expects its larger size will enable it to bid on larger contracts as a prime contractor.
Following the closing of the deal, Kratos will continue to be led by Eric DeMarco, president and CEO, who was previously president and chief operating officer at the former Titan Corp. Prior to DeMarco’s arrival in late 2003, Kratos had no business with DoD. Cooke will assume a new role overseeing all of Kratos’ corporate development and strategic business development initiatives.
Imperial Capital, LLC served as the financial adviser to SYS and Wachovia Securities was the financial adviser to Kratos on the deal.
Singapore Air Force Taps IAC For Advanced Hums For AH-64D Apaches
Intelligent Automation Corp. (IAC) has been selected by Republic of Singapore Air Force (RSAF) for the advanced HUMS (Health Usage Monitoring System) for its AH-64D Apache helicopters.
IAC will adapt and integrate the combat proven IAC-1209, Modern Signal Processing Unit (MSPU) into the RSAF AH-64D aircraft.
The RSAF operates 20 AH-64D and has a reputation of being a “reference customer.”
IAC Chief Executive Officer Jeff Goodrich said, “IAC is extremely pleased to have been selected to support RSAF’s AH-64D helicopters. Our advanced HUMS technology will provide the RSAF with a demonstrated ability to significantly reduce aircraft operating costs, while improving availability and safety.”
IAC is fielding 10 1474 SuperHUMS for the Army’s RQ-7B Shadow 200 Tactical Unmanned Aircraft System, produced by AAI Corp. [UIC], and is approved for CH-47 Chinook helicopters, produced by Boeing [BA]. The SuperHUMs family of products was unveiled last year (Defense Daily, March 7, May 11).
The AH-64D HUMS continuously acquires vital data from aircraft vibration, and health and usage of the engines, transmission, drive-train system, rotor system, and airframe. The IAC system detects and diagnoses potential failures, while recording usage, and providing maintenance personnel with easy to understand corrective actions that can save lives, time, and money. This advanced HUMS also offers continuous Rotor Track and Balance capability, fleet wide health, and performance of safety-critical components, providing advance warning of potential equipment failures.
Northrop Grumman Demonstrates Advanced EHF Satellite Interface With Terminals
Northrop Grumman [NOC] said earlier this month it has demonstrated the interface compatibility of the next-generation Advanced Extremely High Frequency (EHF) military communications satellite with user ground terminals using the new Extended Data Rate (XDR) waveform and protocols.
The tests were conducted using an Army user terminal as well as a terminal configuration to be used by international partners participating in Advanced EHF.
Advanced EHF is a joint service satellite communications system that will provide global survivable, protected and assured communications for high-priority military ground, sea and air assets.
Northrop Grumman’s Space Technology sector is under contract to provide the communications payloads to Lockheed Martin [LMT], the prime contractor for the Advanced EHF system.
The XDR capability and other advanced technologies will allow Advanced EHF satellites to provide 10 times more communications capacity and six times higher channel data rates than the predecessor Milstar system.
“Demonstration of the satellite-to-terminal interface shows that Advanced EHF is able to serve its U.S. and international users with the high-data-rate protected communications that are so critical to today’s warfighter,” Alexis Livanos, corporate vice president and president of the company’s Space Technology sector, said. “We are very pleased to continue on course, with industry and government, in delivering this capability to our customers.”
Earlier testing in May 2006 verified the backward compatibility of Advanced EHF with legacy terminals using Low Data Rate (LDR) and Medium Data Rate (MDR) waveforms. This latest demonstration was conducted using terminals modified for the higher rate XDR capability of Advanced EHF, and demonstrated operation of all three waveforms, LDR, MDR and XDR.
During the course of several weeks, 84 test objectives were demonstrated with the Advanced EHF payload interfacing to XDR-compatible terminals, including the Army’s Warfighter Information Network-Tactical terminal (WIN-T), the international variant of the Secure Mobile Anti-Jam Reliable Tactical Terminal (SMART-T), and Lincoln Laboratory‘s Advanced Universal System Test Terminal (AUST-T).
The test team, sponsored by Air Force Space and Missile Systems Center, was led by Northrop Grumman, and included participants from the Joint Terminal Engineering Office (JTEO), Lockheed Martin, Army WIN-T program, Lincoln Laboratory, and Raytheon [RTN], which makes the terminals.
Other military satellite communications programs, including the Transformational Satellite Communications System (TSAT) and the Enhanced Polar System, also will utilize XDR waveforms.
The Lockheed Martin-led team is currently under contract to provide three Advanced EHF satellites and the mission control system to its customer, the Military Satellite Communications Systems Wing, located at the U.S. Air Force Space and Missile Systems Center, Los Angeles AFB, Calif